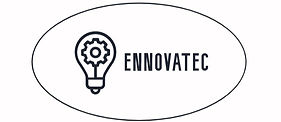
ENNOVATEC
Engineering Innovation & Technology
PROJECT-BASED EXPERIENCE



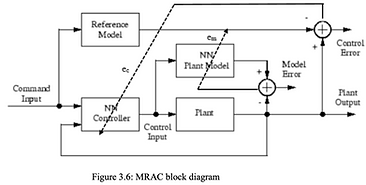

This research project was undertaken as a requirement for my master's degree in mechanical engineering at NC State University. The project aimed to design an intelligent control system that better modeled the non-linearities of the Permanent Magnet Synchronous Spherical Motor (PMSSM), addressing the limitations of linear systems. The research outcomes contributed to the field of non-linear control using neural networks, providing a robust non-linear controller that achieved desired trajectory tracking. As a neural network control engineer in this project, my role was to design, implement, and optimize a data-driven network-based control system for a 9-input, 3-output, and 6th-order non-linear PMSSM.
I performed system analysis to understand the dynamics and behavior of the motor, identifying the key variables, inputs, and outputs. Mathematical models were developed to represent the system dynamics, and I designed the architecture of the neural network, considering the specific control requirements. Data collection and pre-processing were crucial for training the neural network. I collected relevant data from the PMSSM, preprocessed it to remove noise and outliers, and normalized it for better training performance. The neural network was trained using the collected data, and I optimized its parameters using techniques such as backpropagation and gradient descent to minimize the error between desired and actual system responses.
After training, I integrated the neural network into the control system, developing algorithms that effectively utilized the network's outputs to control the motor's actuators. I tested and evaluated the performance of the control system, analyzing its response, stability, robustness, and accuracy. Continuous monitoring allowed me to make necessary adjustments for maintenance and improvement, including periodic and intensive re-training of the neural network or updates to the control algorithms to adapt to changing system conditions.
Through this project, I acquired valuable skills in system analysis, model development, neural network design, data collection and pre-processing, training and optimization, system integration, performance evaluation, and maintenance of control systems. Results from the project included the performance of the feedforward neural network-based inverse model, which achieved a Mean-Squared-Error (MSE) of 0.00053, and the Model Reference Adaptive Controller (MRAC) achieved a performance of 0.000648 MSE for tracking the desired reference trajectory. These results demonstrated the effectiveness of the developed intelligent control system for the PMSSM and its ability to overcome the limitations of previous controllers, such as robustness issues and difficulties in accounting for non-linearities and uncertainties.
Overall, this project empowered me as a neural network control engineer to leverage the capabilities of neural networks and advance the development of intelligent control systems, particularly for non-linear dynamical systems like the PMSSM.
DESIGN OF A INTELLIGENT CONTROL SYSTEM USING NEURAL NETWORKS
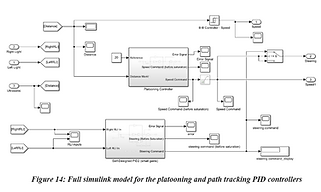


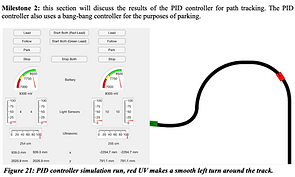
UNMANNED VEHICLE WITH MATLAB/SIMULINK
This project aimed to develop and implement a control system for an Unmanned Vehicle (UV) in a virtual environment. The project consisted of three milestones and a team of two. In milestone one, the team designed a light sensor, an ultrasonic sensor, a DC motor drive, and a Bang-Bang (BB) controller for path tracking and parking. Milestone two involved tuning a Proportional, Integral, and Derivative (PID) controller for line tracking and using the BB controller for parking. The final milestone required designing a second PID controller for platooning with a target distance to follow another UV. The project utilized Matlab and Simulink for the GUI app, track platform, and data recording.
The team designed and implemented various subsystems in Simulink, including the light sensor, ultrasonic sensor, and DC motor. The light sensor configuration included two sensors on each edge of the track, and the ultrasonic sensor was used to detect obstacles. The PID controller was used for precise path tracking, and the platooning PID controller regulated the UV's speed to maintain a constant distance from another UV.
The project's key outcomes were the successful design and implementation of the control systems, including the sensors, motor drive, and PID controllers. The team learned about sensor integration, controller design, and tuning techniques. They also faced challenges with signal processing and motor control, which were resolved with assistance from the teaching assistants. Overall, the project demonstrated the team's ability to develop and deploy a functional control system for an Unmanned Vehicle in a virtual environment.



This project aimed to optimize the design of an Electro-Permanent Magnetic Clamp (EPMC) for machining work holding, using principles of modeling, analysis, and FEMM simulations. The objective was to create a system that provides a holding force of 500 lb with a safety factor of 3.0 (1500 lb). The project focused on optimizing dimensions for poles, cases, and magnet grades, and reducing material costs.
The design process involved Magnetic Circuit Analysis (MCA) to estimate the number of turns needed to flip the polarity of AlNiCo magnets. FEMM simulations were conducted to determine the number of turns and current required. Extensive simulations were performed to optimize the dimensions of poles, magnets, and body cases. The optimized design achieved a weight reduction of over 13 pounds while improving performance and reducing costs.
The proposed design utilized electromagnets, permanent magnets, and a ferromagnetic body to secure the workpiece during the machining processes. The EPMC system consisted of vertically polarized AlNiCo magnets placed within a plastic bobbin and wrapped with magnet wire. NdFeB magnets were positioned in the steel body. Assumptions were made regarding the bobbin dimensions, steel type, and neglected air gaps.
The project successfully achieved the performance objectives of generating a strong magnetic force, allowing easy removal of the workpiece, and optimizing material cost and performance. Multiple FEMM simulations helped identify the key factors influencing the vertical reluctance force and saturation, leading to the determination of optimized dimensions and magnet grades. Overall, this project demonstrated the application of design principles in creating an efficient and cost-effective Electro-Permanent Magnetic Clamp for machining work holding.
​
​